Injection molding is a term that describes the manufacturing process in which large quantities of parts are produced by injecting plastic material in a closed mold. A variety of materials can be used in the process, but the most common one is plastic.
There are many advantages of using this process, and some of them are described below.
1. Highly complex features and small details
This is one of the most appreciated advantages of this process. The plastic injection molds work under high pressure, which results in the plastic being pushed to all the smallest possible parts of the mold as the plastic is pressed hard against the mold. Due to this pressure, you can add the smallest possible details into the mold, and the process will ensure the highest specificity.
Download Branding Resources Guide
Building a brand starts by having the right tools and advice. Download our top 10 essential tools and resources to kick-start your branding.
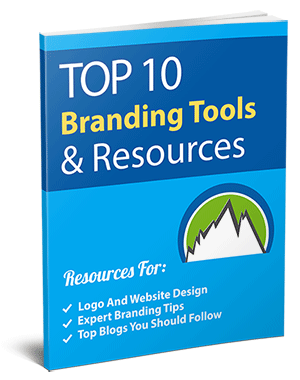
2. Greater efficiency
As the molds are designed per the requirements of the customer and the presses are pre-programmed, the molding process itself is very fast as compared to any other molding process. The plastic injection molding process takes no time and offers more parts to be manufactured by a single mold. The production output rate is one of the things that iscost-effective and highly efficient about this method.
3. More strength
In the plastic injection molding process, there is a possibility to use fillers in the injection molds. The fillers are able to reduce the plastic density while it molds and helps in achieving greater strength to the part that is being molded. So when there is a requirement for the parts to be strong and highly durable, there is an option to add more strength.
4. Multiple plastic types use
This is also one of the things that this process has to offer, and you can use different plastic types in one go. You can achieve this with the help of co-injection molding, so you don’t have to worry about using only one type of plastic.
5. Fast production
You can make many molds in just a matter of an hour, so depending upon the impressions that are in the machine, you can still expect the next output in a matter of a few seconds.
6. Colour and material flexibility
You can change the material and color of the product and can mix different types of plastics as well.
7. Low labor cost
It is a very reliable and automatic machine that works on the process of injection molding without any difficulty and is super efficient and fast. So the parts can be produced without much effort and even no labor.
8. Zero waste
There is zero or minimum waste with this process as the plastic waste is ground up and easily reused.
9. Design flexibility
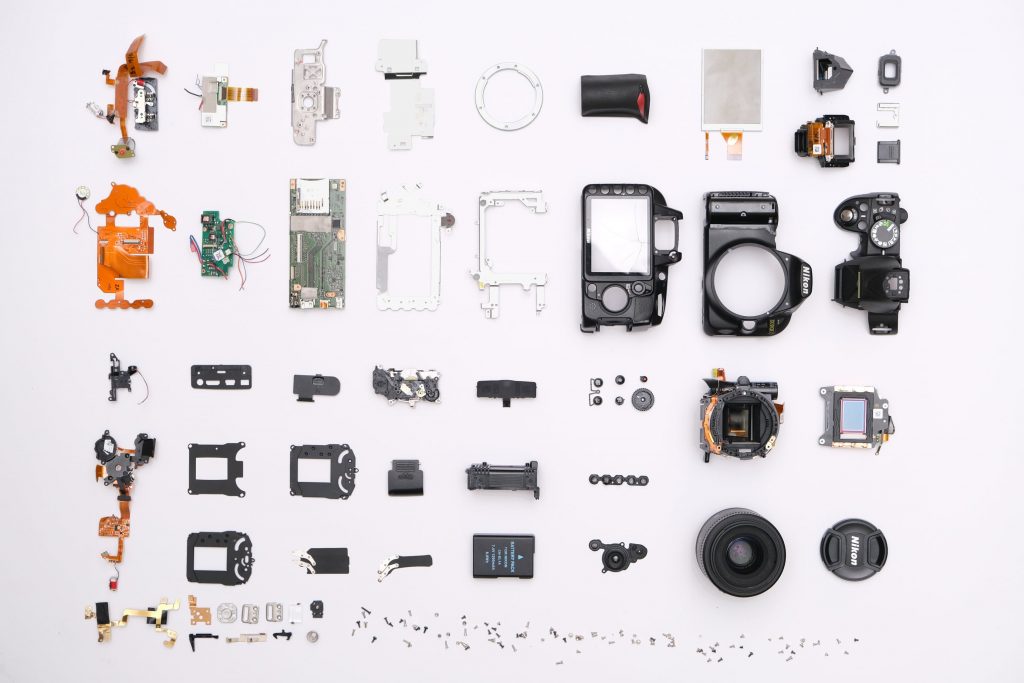
Photo by Kei Scampa in Pexels
There are some restrictions around the design, but there are almost limitless flexibilities when it comes to design, so irrespective of the complexities, plastic injection molding can take care of all designs.
Final Words on Plastic Injection Molding
The plastic injection molding process is usually used for the production of plastic parts, including automobile parts, heavy-duty medical equipment and small instruments, and a lot more. You can design an entirely new product by using the plastic injection molding process. The applications are limitless, but it is much more convenient to get these services from the specialties, so there is no flaw in production. There are many companies offering great services, but Qmolding is one such company that has a great reputation and is known for delivering great plastic injection molding services to its clients all over the world. The company works with other materials as well and can provide you as much flexibility as you need.