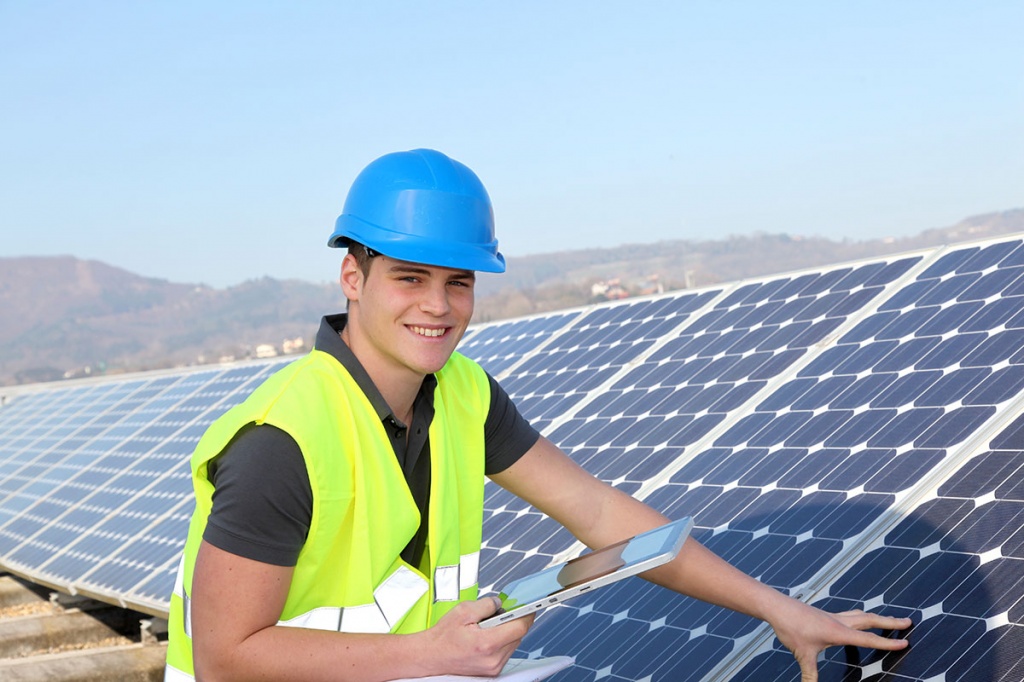
Protection Equipment in Manufacturing Businesses: Ensuring Worker Safety and Business Continuity
Manufacturing businesses are a cornerstone of modern economies, driving production in countless industries, from automotive to electronics, pharmaceuticals, and beyond. However, with the vast array of machines, chemicals, and hazardous processes, manufacturing environments are inherently risky. To safeguard workers from these risks, protective equipment plays a critical role in ensuring their safety, health, and overall well-being. This article explores the importance of protective equipment in manufacturing businesses, the types of equipment commonly used, and how these tools contribute to a safer, more productive workplace.
The Importance of Protection Equipment in Manufacturing
In manufacturing environments, workers often encounter dangerous machinery, heavy loads, sharp tools, hazardous chemicals, and intense physical exertion. Without proper safety measures, the likelihood of accidents, injuries, or even fatalities increases significantly. Protection equipment helps mitigate these risks by providing workers with the necessary tools and gear to protect them from hazards.
Beyond worker safety, implementing proper protective equipment is crucial for maintaining business continuity. Workplace injuries can result in costly downtime, legal liabilities, workers’ compensation claims, and damage to the company’s reputation. The cost of accidents can far exceed the investment in protection equipment. Furthermore, strict health and safety regulations often govern industries with high-risk operations, such as construction, chemical manufacturing, and automotive production. Non-compliance can result in fines, legal action, and even shutdowns, making it vital for businesses to prioritize worker protection.
Types of Protection Equipment Used in Manufacturing
The types of protection equipment required in manufacturing settings can vary depending on the specific risks involved in each environment. However, several categories of safety gear are universally applicable across many industries:
1. Personal Protective Equipment (PPE)
Personal protective equipment (PPE) is a commonly recognized safety gear in manufacturing businesses. PPE protects workers from exposure to physical, chemical, and biological hazards. The main categories of PPE include:
- Head Protection: Hard hats or helmets are essential in environments with a risk of falling objects, head strikes with machinery, or contact with electrical hazards.
- Eye and Face Protection: Goggles, face shields, and safety glasses protect workers from flying debris, chemicals, intense light, and radiation. These are particularly important in welding, grinding, and chemical processing environments.
- Hearing Protection: Earplugs or earmuffs are necessary in noisy environments to protect against hearing loss. Prolonged exposure to loud noises can cause irreversible damage to workers’ hearing.
- Hand Protection: Protective gloves shield workers from cuts, burns, chemicals, and electrical hazards. Gloves made from rubber, leather, or Kevlar are common, depending on the type of hazard.
- Foot Protection: Steel-toed boots protect feet from falling objects, sharp materials, and hazardous substances. They often have anti-slip soles to prevent workplace accidents.
- Respiratory Protection: Respirators and masks are essential in environments where workers may be exposed to airborne contaminants like dust, fumes, or hazardous chemicals. These include disposable face masks or advanced powered air-purifying respirators (PAPRs).
2. Machine Safety Equipment
Many manufacturing businesses rely on heavy machinery to perform cutting, welding, molding, or assembly tasks. To prevent accidents, machine safety equipment is crucial. These include:
- Machine Guards: Physical barriers enclose dangerous parts of machinery, preventing workers from accidental contact with moving parts. Depending on the machinery, these can be fixed, interlocking, or adjustable.
- Emergency Stop Buttons: These are strategically placed on machines and equipment. They allow workers to quickly stop the operation in case of an emergency, preventing injuries or further damage.
- Safety Sensors and Alarms: Safety sensors detect irregularities, such as a worker’s hand getting too close to a moving part, and can trigger an automatic shutdown. Alarms serve as auditory or visual signals to warn workers of potential dangers. In addition to safety equipment, many businesses now invest in long-lasting chassis protection coatings to extend the life of their machinery by shielding metal surfaces from wear, rust, and corrosion, reducing the risk of machine failures and costly repairs.
3. Fall Protection
Manufacturing environments often involve elevated work platforms, scaffolding, or ladders, creating fall hazards. Fall risk can result in serious injuries, but fall protection equipment can prevent such accidents. The main types of fall protection equipment include:
- Harnesses and Lanyards: Workers who work at heights must wear a full-body harness attached to a secure lanyard. These devices prevent falls and reduce the risk of injury.
- Guardrails and Safety Nets: Guardrails around elevated platforms or work areas provide a physical barrier, while safety nets can catch falling workers and prevent them from hitting the ground.
- Anchorage Systems: These systems provide a secure attachment point for fall arrest equipment, ensuring workers are safely tethered to a fixed object.
4. Fire Safety Equipment
Fires are a significant concern in manufacturing environments, particularly those that involve flammable materials or heat-intensive processes like welding. Fire safety equipment is vital to prevent, control, and extinguish fires, and may include:
- Fire Extinguishers: These are strategically placed around the workplace to enable workers to put out small fires before they spread quickly.
- Fire Suppression Systems: Automatic fire suppression systems, such as sprinklers or chemical agents, are integrated into the building’s infrastructure to control fires in their early stages.
- Flame-Resistant Clothing: In environments with a high risk of fire or heat exposure, flame-resistant clothing helps to protect workers from burns or serious injuries.
5. Environmental Safety Equipment
In certain manufacturing settings, workers may be exposed to harmful chemicals, radiation, or environmental conditions such as extreme temperatures. To mitigate these risks, businesses need to invest in environmental safety equipment, including:
- Chemical Spill Kits: These kits contain absorbents, neutralizing agents, and protective clothing to clean up chemical spills quickly and safely.
- Ventilation Systems: Proper ventilation is necessary to remove harmful fumes, dust, and gases from the work environment and maintain air quality.
- Heat-Resistant Clothing: In environments with extreme temperatures, heat-resistant suits and cooling vests help protect workers from heat stress and burns.
The Role of Training in Protection Equipment Usage
While protection equipment is essential in mitigating workplace hazards, it is not enough. Workers must be properly trained to use, maintain, and inspect their protective gear to ensure the maximum safety level. Training programs should cover:
- Proper Use of PPE: Workers must understand when and how to use different forms of PPE and the importance of wearing the right gear for the job.
- Machine Safety Protocols: Workers should be trained to operate machinery safely, understand the importance of machine guards, and react in emergency situations.
- Emergency Procedures: In a fire, chemical spill, or other emergencies, workers must know the correct procedures to follow, including fire extinguishers, evacuations, and first aid.
Conclusion
In conclusion, protection equipment is indispensable in manufacturing businesses, not only for ensuring the safety of workers but also for maintaining operational efficiency and legal compliance. The variety of safety equipment available—from personal protective gear to environmental safety measures—addresses the hazards associated with different manufacturing processes. By investing in protection equipment and providing comprehensive training, manufacturing businesses can minimize the risk of accidents, reduce downtime, and promote a culture of safety that benefits both workers and the bottom line.